Blog #4
- Changyu Lee
- Nov 25, 2023
- 4 min read
Between November 11th and 25th, a lot was done in terms of analysis. Our team possessed a broad concept of our design's appearance, yet it was imperative to verify that each tool incorporated in our design aligns effectively with our constraints. Ensuring that we utilize the most suitable tools from those available was also a crucial aspect of our evaluation. This’ll be elaborated on later in this blog. In addition to these analyses, securing validation structures has been a high priority for us. We have secured permission from HYTORC, a company that makes a lot of bolt torquing equipment, to use their bolt calibration bench to validate our device and application on. Additionally, the University of Houston’s Smart Materials and Structures Lab can provide a large flange that uses 1” diameter bolts. Despite the difficulty of relocating, we can place it in an environment with ambient noise resembling that of workplaces where our device would be utilized. We’re also currently speaking with the university's machinist with the hopes of creating a plated validation structure that may be easier to move around than the large stainless-steel flange.
The design of our handheld device uses a pistol grip to support a solenoid to facilitate tapping, a recorder to capture audio, and a battery pack to provide power to the solenoid. The following figure shows an exploded view of the proposed device:

Within the case, there will be a circuit that connects the power supply and the solenoid to a normally open push button. Pressing down on the button will excite the solenoid and cause the push/pull rod thereinto tap the bolt. The casing of our device will be 3D printed, as that will be the easiest way to manufacture it and the device will not be subject to any substantial forces. The figure below shows the overall design of the circuit for the solenoid:

Insofar as our analyses directly related to our problem go, we looked at sound volume as well as feature extraction ability. While other analyses were done in terms of battery life, these two constraints are the ones most directly related to how well the device will perform percussion monitoring on bolts. We first performed the sound analysis to compare a few different solenoids as well as a hammer to see which tools among them best fit the project.
This was done by tapping on a bolted flange (with bolt OD of 1” each) and looking at both average and peak decibel levels therein. This was done on a 16-bolt flange, and each device was tested on each bolt. To examine the average and peak audio levels, tapping was done in 10-second intervals. After we gathered the 16 sets of data per device, we averaged them and used those numbers to determine which among the devices should be considered further.


It should be noted that while solenoid 3 met our sound constraints, unfortunately its spring was very loud, and that noise overshadowed the tapping, rendering it useless for our project’s purposes. As such, audio analysis was done exclusively with solenoid 2 and the hammer to determine which among these tools gathered better features. This wasn’t done in relation to our constraints but was rather a comparative analysis between the solenoid and hammer as well as the phone and an audio recorder that the team bought. This was done by looking at power spectral density, or power per unit frequency associated with the sound. In effect, a machine learning algorithm would look at the peaks where power is. The first comparison was done tapping on a flange’s bolts using both the hammer and the solenoid. All audio for this specific test was recorded using the Voice Memo application on an iPhone.
We found that while the hammer extracted more features, the solenoid was able to produce audio with a larger magnitude in terms of feature differences. Normally, in percussion research, the researchers can pick and choose features, but these features are going to need to be very distinct if the application is to pick features on its own. As such, higher average magnitude distances will be exceptionally important, and the solenoid is better than the hammer in this regard. The figure below shows the analysis data for the hammer vs solenoid:

Additionally, the iPhone was compared to the audio recorder we bought. The important thing here is having “clean data” or minimizing the amount of noise around the prominent peaks to avoid confusion in the algorithm. In this regard, the recorder provided better data and as such is the choice we went with for our final design. The figure below shows the analysis data for the recorder vs phone:
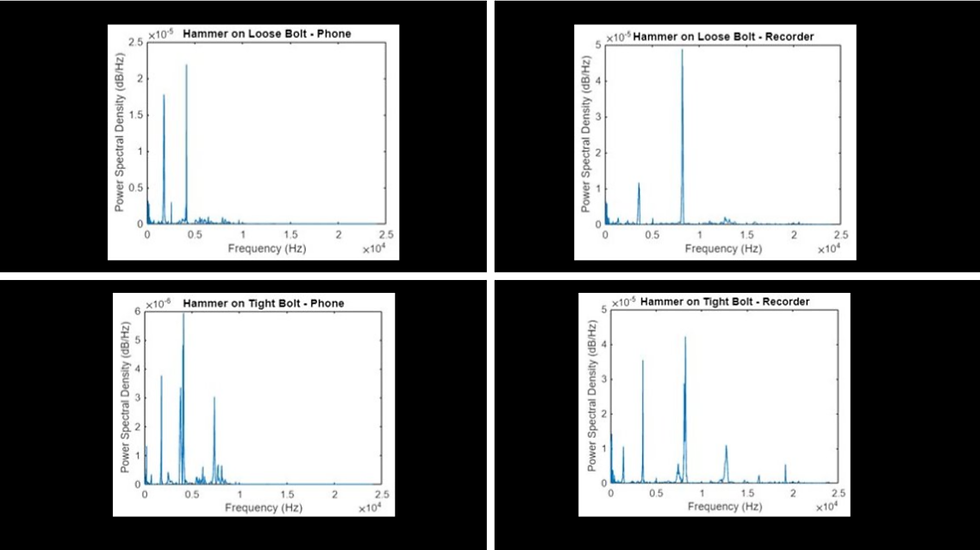
For the coming semester, the team have all the necessary components for constructing the device, and the only things we need to order are a few items related to validation. We are talking with UH’s machinist to talk about a very simple job – machining four through holes into two metal plates in order to use a stand constructed by the university’s Smart Materials and Structures Lab. Aside from that, we can use a flange that has 1” bolts and bring it into a commercial environment for further testing. Finally, we have been given permission to use a bolt calibration bench at HYTORC, which has bolts which go up to 4” in diameter.
Comments