Blog #8
- James Valentine
- Apr 13, 2024
- 3 min read
The main parts of the new second iteration of the 3d printed casing have now been printed and assembled. This new device is now fully functional in respect to producing and gathering data required for bolt torque analysis. The new casing features several fixes and improvements from the first design. The previous casing had an issue of the screw holes not being big enough, along with some parts possibly blocking the recorder’s mic, all of which had been fixed. In addition, an issue of the recorder interacting with the exposed wires in the body of the device was also resolved by the new integrated wire cover, with the recorder casing modified to reflect those changes.
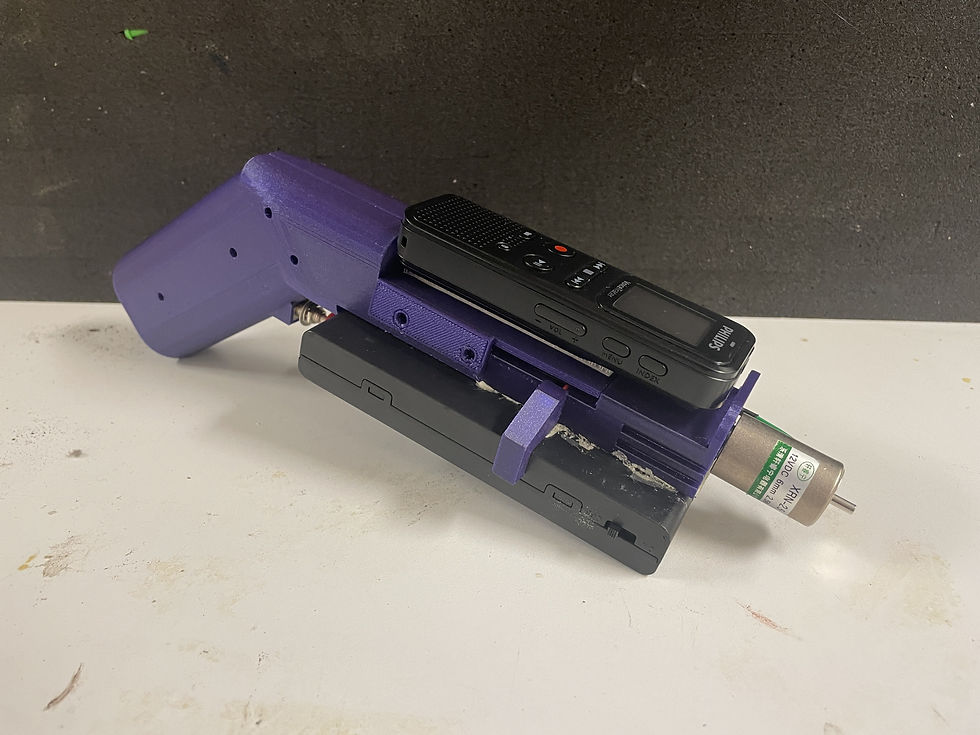
The application has also gone through a few changes to achieve better accuracy. After following advice from Dr. Agrawal and comparing MFCC matrices, it was found that the difference therein might not be significant enough unlike what was previously thought. Following a meeting with Dr. Gangbing Song, who has a lot of experience in percussion monitoring, the team pursued using Power Spectral Density instead. Through combining this feature method with a linear regression algorithm, accuracy was increased to 70%. This is the highest combination of audio features and algorithm that the team has found thus far, and this is reflected in a new final design for the application.
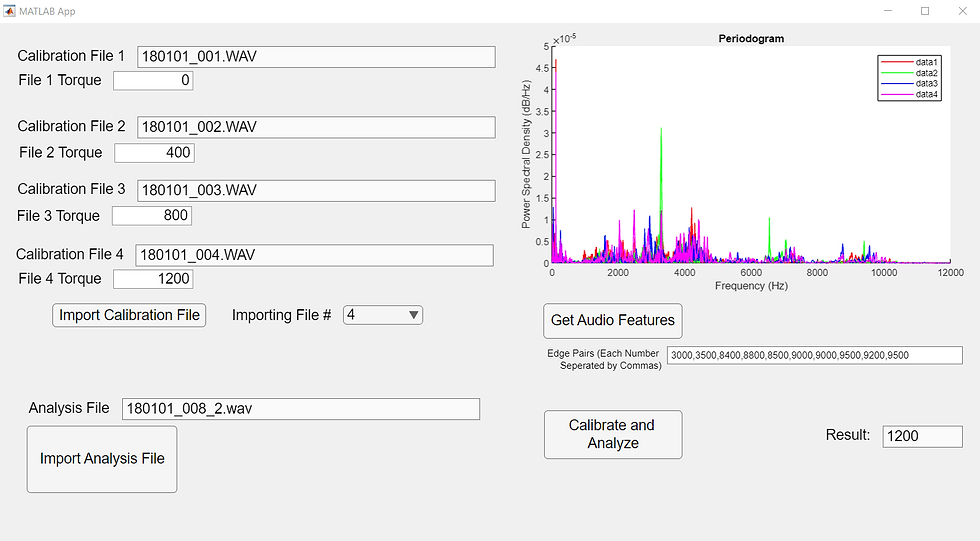
With this, use of the app is made a bit more complicated. Instead of just uploading audio and clicking the analyze button, the user needs to identify frequencies where the audio is different. This isn’t expected to be hard, as all the user will need to do is click the “get audio features” button and then see where the periodogram peaks are different when it’s plotted for all four calibration files.
The team has also performed more validation, and now the analysis time constraint has been fulfilled, as shown in the following table. This only leaves ease of use to be validated further.
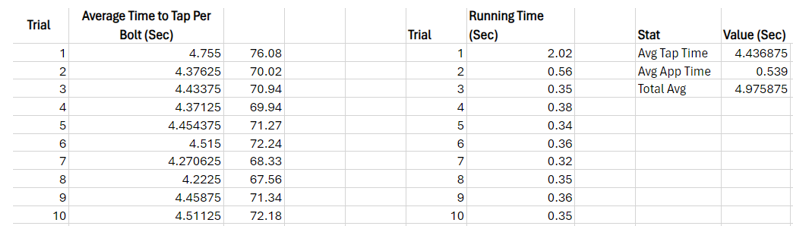
Overall, we believe that our project is almost successful. It has met just about every single constraint we set other than bolt assessment accuracy and ease of use (with ease of use yet to be tested). Regardless of how well it performs in vectors such as proper sound volume or dimensional constraints or battery life, if the device is not accurate enough in assessing the bolts, then the device fails to properly meet the problem set out by our team in the fall.
Nonetheless, the team aims to continue improving the project as the academic year ends. Regarding the physical device, the newly integrated wire cover and recorder casing is expected to be tested and modified to best fit the device. The device will then undergo testing to ensure user friendliness. From the results of these tests, the impact gun will then be examined again for the possibility of improvements, along with any required fixes for issues found.
Improvements to the application have already been made, but it will continue to undergo constant tweaking to try to achieve the 85% accuracy constraint. The team would theoretically like to pursue deep learning algorithms as an option for machine learning algorithm choice, as this would almost certainly enhance accuracy results, but the time it would take to get this done is likely too much to fit in before the project time ends.
The only constraint left to be validated will be ease of use. The device, application, and instruction pamphlet will be given to multiple people to see if they can understand and perform several tasks, and the results will be presented in our technical report.
Additionally, the team has been drafting a technical report poster, as can be seen below.

Comments