Blog #3
- James Valentine
- Nov 11, 2023
- 5 min read
The first item of concern right now is the work the team’s done through 10/28 to 11/11. Most notably, CAD drawings of the solution have been created. In conjunction with the audio analysis, two rough concepts were modeled: one was a solution design that would use a hammer for tapping on the bolts. The other design used a solenoid for tapping instead.

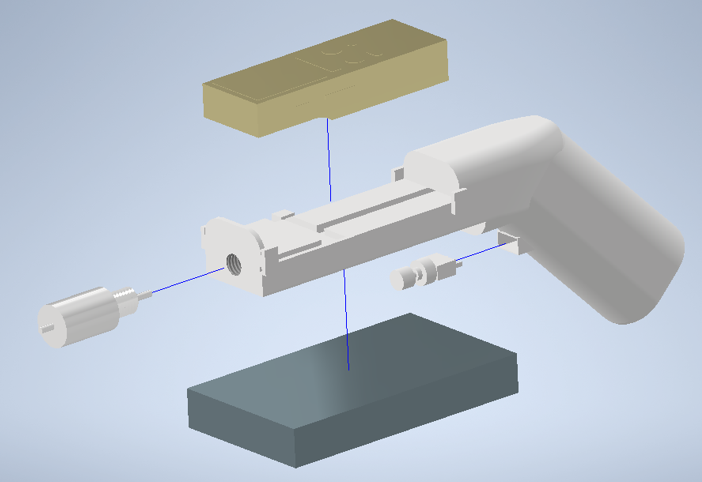
The hammer design would secure the audio recorder to an apparatus that would be affixed to a hammer. This design is relatively simple compared to the solenoid-enabled design. The solenoid design uses a pistol-grip-esque design to support the audio recorder as well as a circuit designed to excite a push-pull solenoid. This includes the AA-enabled power supply (which is the dark grey brick on the picture above), a button which will be placed on the grip, and a push-pull solenoid placed at the end of the device. The audio recorder will be placed next to the solenoid to ensure that audio is picked up clearly.
In addition to making progress with CAD, the team performed audio analysis of multiple recording devices as well as comparing tapping data gathered with a hammer and a solenoid. This analysis involved using data and a flange structure provided by the University of Houston’s Smart Materials and Structures Lab. In terms of the team’s usage of the flange, all of the bolts on the flange were loosened to 0 ft-lb of torque, and data was gathered. Two comparisons were made: one compared the recorder that the team bought with the voice memo app on iPhone. The other was between audio features from audio gathered using a hammer and a solenoid. Due to shipping issues, data from the solenoid was provided by the UH MECE lab. It was confirmed that the data was gathered with the same model of solenoid and this data was compared to data gathered with a hammer on the same flange and under the same recording circumstances. Essentially, the team looked at power per unit frequency at sound data gathered with different tools, and examined where the power peaked in all of them. If the peaks had large differences in magnitude and didn't have a lot of surrounding noise, then the audio was considered better for classification.


Ultimately, the team found that the recorder and the solenoid gathered features better for analysis than the iPhone and the hammer, respectively. The team already knew that an audio recorder other than an iPhone would be used, as different iPhone models have different sizes and making a device that could accommodate the various sizes was deemed to take too long given the scope of this project and the other work that needed to be done on the design. Confirmation that the recorder that was ordered was better than the iPhone, however, was needed and ascertained here. Additionally, determining that the solenoid is better than the hammer solidified that a solenoid-enabled design for the project would be pursued.
In addition to figuring out the design of the physical, handheld device, the design of the MATLAB application has been taken into consideration. The team already has code for analysis of audio data and for machine learning algorithms, but the application needs to be planned. An understanding of how the users will interface with the data is needed in addition to ways to communicate how the code will perform audio analysis. For both of these, block diagrams were made. These outline the general flow of code given specific actions taken by a user that is using the application the team will make.

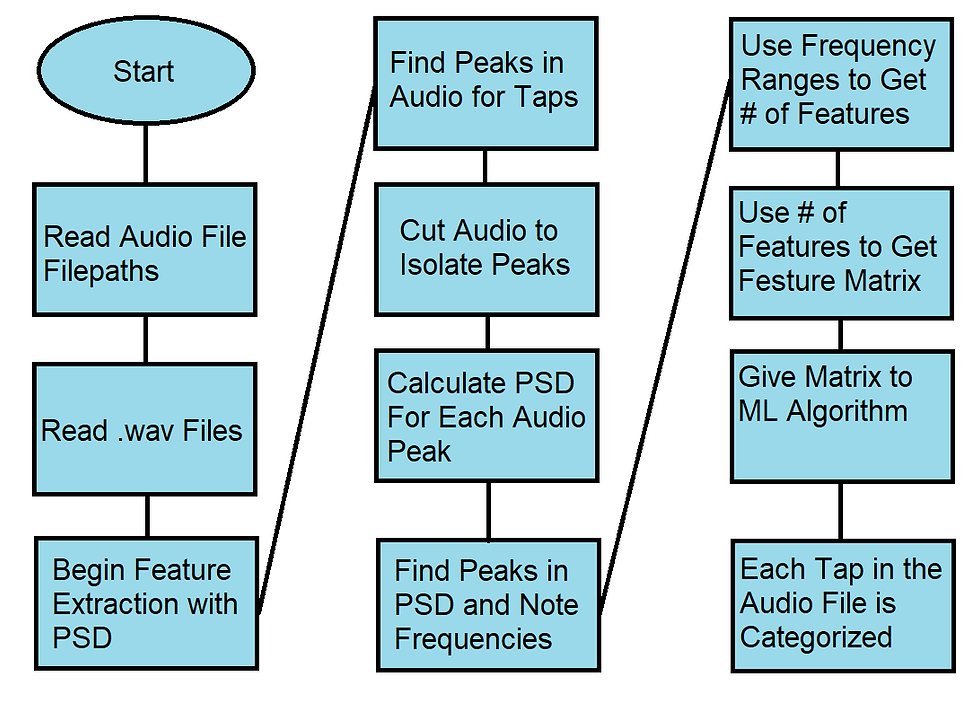
From November 11th to the 18th, the design team’s primary objective is to complete Milestone 2. This phase primarily involves utilizing the current CAD design to conduct diverse Finite Element Analyses using various types of 3D filament materials. These analyses are essential for determining the most suitable filament to be used for the final prototype. Simultaneously, the team will also dedicate efforts to strategically plan the user interface and functional aspects of the application design.
Moving into the latter part of this timeframe, from November 18th to the 25th, the design team will transition into Milestone 3. This crucial phase entails the procurement of necessary components and materials essential for commencing the fabrication process. This careful preparation ensures a smooth transition from the design phase to the physical realization of the project.
It is likely that the CAD designs will require further revision, so this will also be taking place soon.
Unfortunately, the team has faced a few different obstacles throughout project work. In recent weeks, our design team faced a significant scheduling challenge, starting with an unexpected delay in delivery of the solenoid we had ordered for our prototype. Originally anticipated to arrive in time for the completion of CAD drawings, the solenoid’s delivery date was later revised. Consequently, the completion of CAD drawings experienced a two-week setback, finally reaching finalization earlier this week. This incident has raised concerns regarding potential future challenges, especially as we approach the initiation of Milestone 3, where the procurement of prototype materials is on the horizon. The inherent risk lies in the possibility of certain materials encountering prolonged delivery times compared to others. However, our team has strategically planned the project timeline, with the physical prototype not slated for production until mid-December. This deliberate timing provides us with a comfortable buffer, ensuring adequate time for all materials to arrive without compromising the overall progress of our project.
Another challenge we suspect will arise soon is the impending Design Review Report - the final deliverable for this semester which demands our utmost dedication. Recognizing its potential to consume a substantial amount of our time, we are keenly aware of the possible impact on both our other academic commitments and the tasks earmarked for Milestone 3. To address this challenge proactively, our teams have devised a strategic solution. We intend to break down the report into manageable sections and assign specific deadlines for each, along with identifying team members responsible for overseeing their completion. The overarching aim is to have the entire report finalized two days in advance of the submission deadline, mitigating the risk of last-minute hurdles and ensuring a smooth progression of our project alongside our academic responsibilities.
Lastly, the ultimate challenge looming is the acquisition of a suitable validation structure crucial for evaluating the efficacy of our device. Presently, our team is diligently navigating the process of obtaining quotes from various used metal shops and reaching out to companies in hopes of securing permission to utilize a bolted structure for rigorous testing. The team currently has five potential vendors, but not all of them give quotes over the phone, so there is a process of waiting involved here. After the team has quotes on prices for flanges, they will be given to Dr. Gangbing Song, who will try to secure funding for it from the University of Houston.
The team is also in contact with the University of Houston's machinist to talk about machining a custom validation structure.
Comments